Interview with SDR Packaging
Nicolò Ferracin, sales manager and GM of SDR Packaging, tells Converting magazine about his positive experience with Uteco and our flexographic machines:
Why flexo? And why Uteco?
Flexography allows us to print with efficiency, economy and quality 1000 meters “to infinity” runs, managing up to 50 jobs a day. As for the choice of the supplier, it arises from the need for customization: we had special technical needs and Uteco was very good at welcoming and realizing them, implementing new developments that have increased our and their know-how. The first machines are from 15 years ago and are still working perfectly, and today we have five, all equipped with 1100 web to be able to manage jobs with maximum freedom, of which four are 10 colors machines (two of these equipped with a roto group for coating with glossy and matt paint) and one 6 colors machine to process easier jobs more efficiently. With this fleet we always have white, black and pantones ready; we have machines dedicated to internal printing, external printing, soft touch paint, etc. With Uteco we have brought to our company the innovations in which they have always been at the forefront, on machine control and color management to boot.
What are the benefits of Uteco's technology?
Many and at various levels. I'm thinking, just to make a macroscopic example, of the reliability that allows you to manage dozens of job changes a day, getting up to register and then into production in a very short time. And how much that counts can be easily seen just by considering that we print one thousand meters runs in 10 minutes in average, half of the machines in SDR are currently in downtime to set up new jobs.
Wouldn't a digital be useful?
When all is said and done, running costs, consumables first and foremost, are still too high.
So we return to the flexibility of flexo, with its organizational and economic advantages…
But also, in the case of Uteco, energy efficiency, and therefore once again sustainability, as well as production speed. In addition, this manufacturer has always worked to improve the working environment, reducing noise pollution with the isolation of moving groups, and redesigning the upper deck, color stations, suction system… In SDR we
have obtained all of the ISO quality certifications and Uteco has always met our expectations perfecting machines according to the various objectives.
Without neglecting the, often underestimated, aesthetic factor.
Aesthetic factor? You mean the appearance of the machines?
Yes. We spend so much of our lives at the plant, I do not understand those entrepreneurs who live in sumptuous houses and drive beautiful cars but work in ugly and neglected factories. Uteco was the first to work on the appearance of its machines that, in fact, look great in our plant and really enhance it. It changes the lives of the people who work there and communicates the care we put into the work, which in turn becomes care of the product and the customer.
In short, Uteco machines are an added value in terms of reputation as well…
Undoubtedly; in fact, our collaboration has extended beyond technical aspects. For years, for example, they brought their foreign clients to us to show them the operating machines, and it was a satisfaction for us knowing that our beautiful and tidy, clean and well-organized departments were talked about all around the world.
Someone even came back with their own people to show them how the work should be done. And when, until not long ago, customers used to come to the plant for start-ups on board the machines, it was a pride to exhibit such beautiful machinery.
Are you planning new investments in machinery?
To best serve large groups that work on long runs, and therefore also ask for the highest quality consistency, we may equip ourselves with a rotogravure machine. We are also pushing towards work automation: recently, the first in Europe to do so, we set up a robotic system for the automatic assembly of clichés and, more generally, we are studying how to reduce off-line set-up times.
With an expectation that Uteco can satisfy: automation must also make the machine easier to use, reducing staff training times and, consequently, dependence on the availability of trained labor.
Both because there are fewer and fewer people interested in factory work, and because changing employers, places and even jobs today is much more frequent than it was in the past, and companies must put themselves in a position to manage a fast-paced turnover of their work-force. Especially if they produce 2 million meters of material per week like we do.
To read the full article click here and turn to page 40.
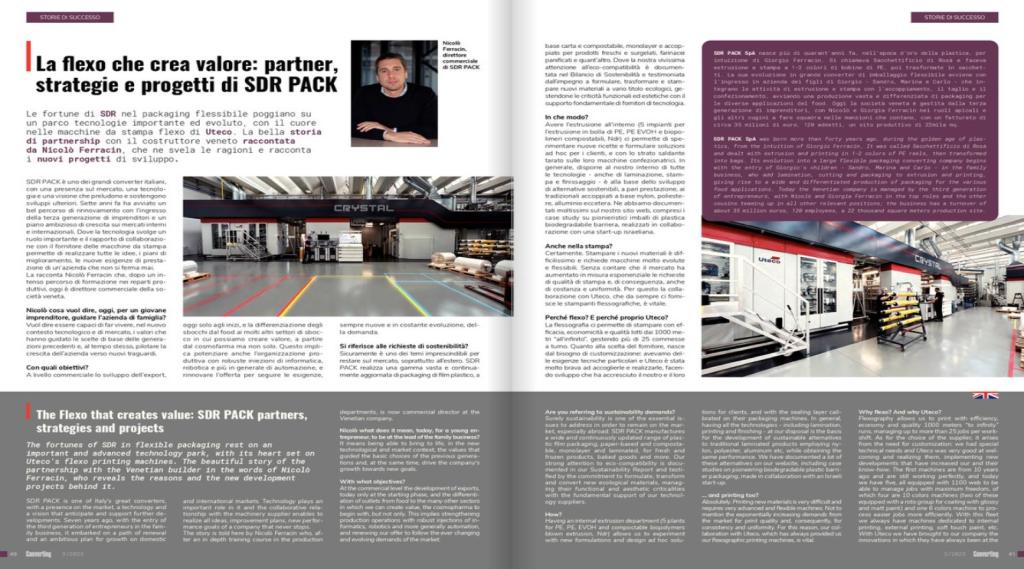